Segundo episódio | Segurança dos Alimentos: a estratégia Domino's Ainda seguindo no assunto de...
Modelo de planilha FMEA
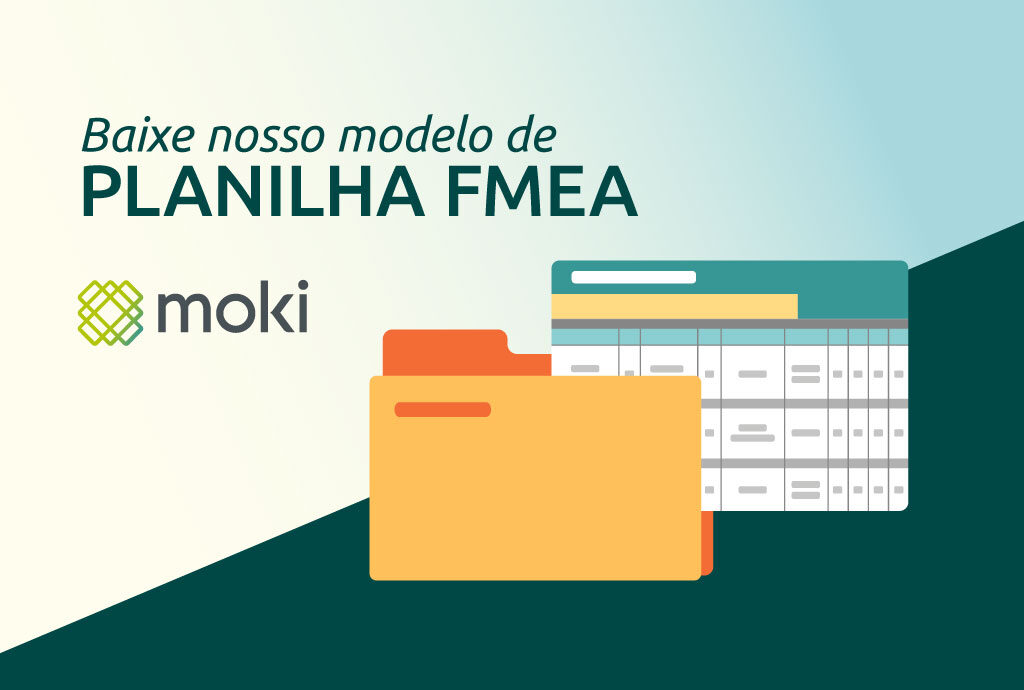
FMEA ou Análise de Modos de Falha e Efeitos é uma metodologia que ajuda a identificar e prevenir potenciais falhas ou riscos que podem ocorrer no processo industrial.
O FMEA pode reduzir a frequência dessas falhas e, consequentemente, potencializar a sua economia, melhorando a qualidade de seu produto e a satisfação do cliente.
O "modo de falha" - forma como um processo é levado a operar de forma eficiente - é composto por 3 elementos: efeito, causa e detecção. São esses elementos que ajudam a realizar o cálculo do FMEA.
Baixe a planilha de cálculo do FMEA gratuitamente aqui!
Comentários